Unbelievable Info About How To Know If PWM Or DC

Decoding the Current
1. Understanding the Basics
So, you're staring at a circuit, maybe a fan controller, or perhaps something a little more mysterious, and you're asking yourself: "Is this thing spitting out PWM or DC?" It's a common question, and thankfully, it's one we can answer. Think of it like trying to figure out if you're dealing with a steady stream of water (DC) or a series of quick bursts (PWM). The difference is crucial for understanding how the circuit behaves and how to troubleshoot it when things go south. Dont worry, it isnt rocket science.
Direct Current (DC) is the straightforward type. Its a constant, unidirectional flow of electrical charge. Imagine a battery it consistently delivers power in one direction. Think of it like a garden hose with a consistent water pressure. The voltage is steady, and the current flows smoothly. This is what powers many of our everyday gadgets.
Pulse Width Modulation (PWM), on the other hand, is a bit more sophisticated. Its a technique used to control the amount of power delivered to a device by rapidly switching the current on and off. The "width" of the pulse (the "on" time) determines the average voltage supplied. So, a longer "on" time means more power, and a shorter "on" time means less power. Imagine flickering a light switch very, very quickly to dim the lights; thats kind of the idea, though far more precisely controlled.
Why do we even use PWM? Because it's an efficient way to control the power going to something like a motor, a fan, or even an LED. Instead of wasting energy as heat (like a resistor would), PWM simply switches the power on and off, allowing for precise control and improved efficiency. Consider it a smart way to dim a lightbulb without turning it into a space heater!
2. Spotting the Difference
Okay, enough with the theory. Let's get practical. The first thing you can do is look for visual clues on the circuit board or within the device itself. Many devices that use PWM will have components designed to handle the rapid switching. Unfortunately, sometimes these aren't obvious. However, there are key aspects we can focus on.
Examine the components. Are there large capacitors near the power output? These are often used to smooth out the voltage fluctuations caused by PWM. It's like putting a small reservoir in that garden hose analogy; it helps even out the pressure. Also, look for chips labeled as "PWM controller" or "motor driver." These are dead giveaways that PWM is in use. Often these chips will have a data sheet available, a gold mine of information regarding the current being produced.
Consider the devices function. Is it a fan whose speed needs to be adjustable? Or an LED whose brightness needs dimming? Or a motor requiring torque control? These are all common applications for PWM. If the device has a variable control knob or software setting for adjusting these parameters, there's a high probability PWM is involved. DC systems usually have on/off capabilities, where PWM offers greater control and variable functionality.
Sometimes, the manufacturer's documentation will clearly state whether the device uses PWM or DC. Check the product specifications, user manuals, or datasheets. If you're lucky, the answer will be right there in black and white. It's always a good first step before delving into more complex methods.
3. The Oscilloscope Advantage
If you really want to know for sure, and you have access to one, an oscilloscope is your best friend. An oscilloscope allows you to visualize the electrical signal in real-time. It's like having X-ray vision for electricity!
Connect the oscilloscope probes to the output of the power supply or the device you're testing. If it's DC, you'll see a flat line representing a constant voltage. Easy peasy. If it's PWM, you'll see a series of pulses rectangular waves that switch between high and low voltage levels. The higher the pulse, the greater the on-time. Measuring the frequency of these pulses is another useful skill, as PWM often operates at very specific frequencies.
The oscilloscope's display will clearly show the duty cycle of the PWM signal. The duty cycle is the percentage of time the signal is "on" compared to the total time of one cycle. A 50% duty cycle means the signal is on half the time and off half the time. By observing the duty cycle, you can understand how the power is being controlled. Playing around with the time and voltage scales on the oscilloscope will help in getting a clearer reading.
Keep in mind that some devices may use a combination of PWM and DC. For example, a device might use PWM to control the average voltage, but then use a DC filter to smooth out the voltage fluctuations. In these cases, the oscilloscope will show a slightly "dirty" DC signal with small ripples caused by the PWM. If the ripples are significant, it is likely PWM. If it's mostly a straight line, it is most likely DC.
4. Multimeter Magic
Don't have an oscilloscope? No problem! A multimeter can also provide valuable clues, although it's not as precise. The multimeter measures average voltage, so it won't show you the individual pulses of a PWM signal, but it can give you an indication of the overall voltage level.
Set your multimeter to measure DC voltage, and connect the probes to the output of the power supply or the device you're testing. If it's DC, the multimeter will show a steady voltage reading. If it's PWM, the multimeter will show an average voltage that's proportional to the duty cycle of the PWM signal. For example, if the PWM signal has a 50% duty cycle and a peak voltage of 12V, the multimeter will read approximately 6V.
One limitation of using a multimeter with PWM is that the reading can be affected by the multimeter's internal filtering. Some multimeters have better filtering than others, which can lead to different readings for the same PWM signal. Also, the frequency of the PWM signal can affect the reading. Higher frequencies may be filtered out more effectively, resulting in a lower average voltage reading. Its a good habit to always refer to your multimeter's data sheet to understand the filter capabilities.
If you suspect PWM, try varying the control knob or software setting that adjusts the power. If the multimeter reading changes significantly as you adjust the control, that's a strong indication that PWM is being used. A stable reading that barely fluctuates suggests DC is at play. But always consider that the multimeter shows average voltage, where an oscilloscope will show you the entire picture.
5. When Things Get Tricky
Sometimes, the situation isn't so clear-cut. You might encounter circuits that use a combination of PWM and DC, or that employ more advanced techniques to control the voltage. In these cases, identifying the type of signal can be more challenging, but not impossible.
One technique is to use a low-pass filter to smooth out the PWM signal before measuring it with a multimeter. A low-pass filter allows DC components to pass through while attenuating high-frequency components, such as the PWM pulses. This can give you a more accurate reading of the average voltage. You can even build your own low-pass filter with a resistor and a capacitor. It's a fun little project that can be very helpful.
Another approach is to analyze the circuit diagram (if you have one). The diagram will show you the components used in the circuit, which can provide clues about the type of signal being used. Look for PWM controller chips, motor drivers, and other components that are commonly used with PWM. The presence of these components strongly suggests that PWM is involved.
Finally, don't be afraid to experiment! Try connecting a small DC motor or LED to the output of the circuit and see how it behaves. If the motor's speed or the LED's brightness can be smoothly adjusted, it's likely that PWM is being used. If the motor only turns on and off at full speed, it's more likely to be DC. And if all else fails, consult with an experienced electronics technician or engineer. They can help you troubleshoot the circuit and identify the type of signal being used. This is a good step to take before you accidentally fry your circuits or components.

Frequently Asked Questions (FAQs)
6. Q
A: While some high-end multimeters have frequency measurement capabilities, they are often not accurate for PWM signals. An oscilloscope is much better suited for measuring the frequency of a PWM signal.
7. Q
A: If the LED's brightness can be smoothly adjusted, it's likely that PWM is being used. You can also try waving your hand quickly in front of the LED. If you see a flickering effect, that's a sign of PWM. The faster you wave, the more prominent the flicker.
8. Q
A: PWM is used in a wide variety of applications, including power supplies, audio amplifiers, and even certain types of heating elements. Essentially, anytime you need precise control over power delivery, PWM is a good option.

Speed Control Of A DC Motor Using PWM, 54 OFF

Dc Motor Pwm Diagram Power Supply Circuit
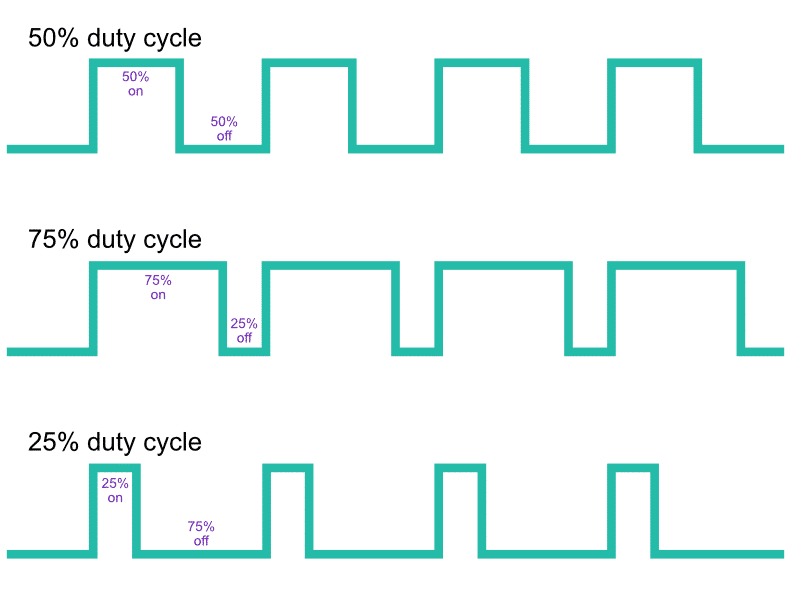